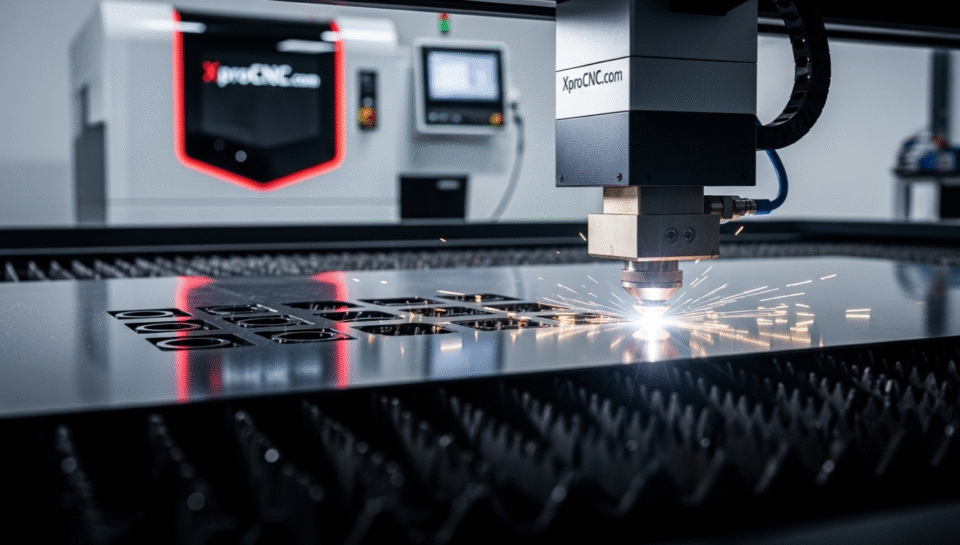
Choosing a new fiber laser cutter for your business is a major investment. While it’s easy to get caught up in the size of the cutting bed or the speed of the gantry, the single most important decision you’ll make is selecting the right laser power (wattage). This choice goes far beyond just the thickness of the metal you can cut; it directly impacts your shop’s efficiency, cut quality, operational costs, and ultimately, your return on investment (ROI).
Making the wrong choice can leave you with a machine that’s too slow for production runs or overpowered and inefficient for the delicate work you do most often. But getting it right means you’ll have a competitive advantage that pays dividends for years.
This guide will walk you through how to think about fiber laser power not as a raw number, but as a strategic business decision. We’ll help you match the right wattage to your specific applications so you can purchase with confidence.
Why Wattage is More Than Speed: The ROI Factor
For a small or medium-sized business (SMB), every dollar counts. The power of your fiber laser, measured in kilowatts (kW), is the engine of your productivity. A higher wattage generally means faster cutting speeds, especially on thicker materials.
Consider this: if you can cut a part in 30 seconds with a 6kW laser instead of 90 seconds with a 2kW laser, you’ve just tripled your potential output. For a growing shop, that increase in capacity is how you take on more jobs, shorten lead times, and increase revenue without needing a second machine.
However, higher power also comes with a higher initial investment and potentially higher operating costs. The key is finding the “sweet spot” where the machine’s capability perfectly aligns with your current and future business needs.
The Core Relationship: Power, Material, and Thickness
The fundamental question that laser power answers is: “What can I cut, and how fast?” The interplay between wattage and material thickness is the most critical factor. Here’s a practical breakdown of what to expect from common power ranges.
Power Range | Common Materials & Max Thickness (Clean Cut) | Best For… |
---|---|---|
Low Power (1kW – 2kW) | Steel: up to 1/2″ (12mm), Stainless: up to 1/4″ (6mm), Aluminum: up to 1/4″ (6mm) | Intricate designs, thin sheet metal, shops focused on precision over high-volume output. |
Mid Power (3kW – 6kW) | Steel: up to 1″ (25mm), Stainless: up to 1/2″ (12mm), Aluminum: up to 1/2″ (12mm) | The “all-rounder.” Excellent for general fabrication shops cutting a wide variety of thicknesses with high efficiency. |
High Power (8kW+) | Steel: 1″+ (25mm+), Stainless: 3/4″+ (20mm+), Aluminum: 3/4″+ (20mm+) | Heavy industrial production, thick plate cutting, and maximizing throughput for large-scale orders. |
(Note: These values are general estimates. Actual performance depends on material grade, gas type, and machine quality. Always request a test cut on your specific material.)
Application Guide: Matching Power to Your Industry
Customers buy solutions, not just machines. Let’s move beyond specs and look at how wattage applies to real-world industries across Canada and the USA.
For Custom Sign Makers & Metal Artists
Your work is defined by precision and edge quality. You’re likely working with thinner gauge steel, stainless steel, and aluminum.
- Recommended Power: 1kW – 2kW. This range offers exceptional control for cutting intricate letters and complex patterns with a flawless edge finish. A higher-power machine might be too aggressive, risking damage to delicate parts. A machine like this provides all the capability you need without the cost of a high-power unit.
For General Fabrication & Job Shops
Your business thrives on versatility. One day you’re cutting 22-gauge steel brackets, and the next you’re processing 1/2″ aluminum plates. You need a machine that can do it all, efficiently.
For Automotive & Aerospace Parts
Your clients demand speed, precision, and repeatability, whether for prototypes or production parts. You might be cutting specialized alloys or thicker structural components.
- Recommended Power: 4kW – 8kW. Speed is critical in these competitive industries. A 4kW or 6kW laser can handle the majority of parts with excellent speed. If your work involves thick structural components or you’re competing for high-volume contracts, an 8kW+ machine provides the raw production power needed to stay ahead.
Beyond Wattage: Other Factors in Your Decision
While power is the main event, a few other factors are critical for performance.
- Assist Gas: The type of gas used (Nitrogen, Oxygen, or shop air) dramatically affects speed and edge quality. High-pressure Nitrogen is used for a clean, oxide-free edge on stainless and aluminum, while Oxygen is a faster, more cost-effective choice for carbon steel. Ensure the machine you choose can handle the required gas pressures for your applications.
- Machine Build & Support: A powerful laser source is useless if the machine’s frame and gantry can’t move it accurately at high speed. A rigid, well-built machine ensures that you can actually use the power you paid for. Furthermore, as a Canadian business, we at XproCNC.com understand the need for reliable, accessible North American support to keep your operations running smoothly.
- Software: Your CAM software must be able to properly program the advanced features of a modern fiber laser, including fly-cutting, lead-in strategies, and kerf compensation. For a deeper dive, read about the differences between leading software like Mastercam vs Fusion 360.
Making the Right Choice for Your Business
Choosing the right fiber laser power is a balancing act. Start by analyzing the work you do today—what materials and thicknesses make up 80% of your jobs? Then, think about the work you want to win tomorrow. Investing in slightly more power than you need right now can be a smart move that allows your business to grow.
Don’t just rely on spec sheets. Talk to an expert who understands your business goals and can help you analyze the true cost and benefits of different power levels.
If you’re ready to see how the right machine can transform your shop’s productivity and profits, contact the XproCNC team today. We’re here to help you find the perfect solution for your needs.
Disclaimer: The information provided in this blog post is for informational purposes only. The performance of any CNC machine can vary based on specific materials, machine configuration, software, and operating conditions. You should always consult with a qualified expert and conduct material testing before making a purchasing decision or operating machinery.