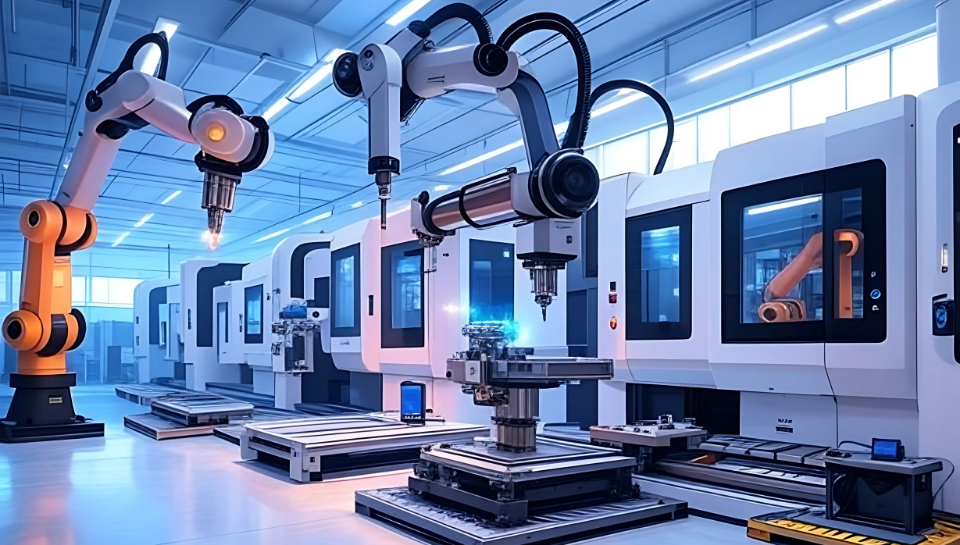
The CNC machining industry is at a pivotal moment. As we approach 2025, advancements in technology, shifting market demands, and a focus on sustainability are driving transformative changes. From small shops in Canada to large-scale manufacturers in the United States, businesses are adopting cutting-edge CNC technology to stay competitive. Whether you’re a shop owner, engineer, or industry enthusiast, understanding the CNC trends 2025 will help you navigate the future of CNC manufacturing. In this article, we explore the top trends shaping the industry, backed by proven innovations and market insights, to keep you ahead of the curve.
AI-Powered CNC Machining: Smarter, Faster, Better
Artificial intelligence (AI) is revolutionizing CNC machining by making machines smarter and more efficient. In 2025, AI in CNC will take center stage, enabling predictive maintenance, adaptive machining, and optimized toolpaths. For example, AI algorithms can analyze real-time data to predict when a spindle might fail, reducing downtime by up to 30%, according to industry studies. This means North American manufacturers can save thousands in repair costs and keep production humming.
AI also enhances precision. Adaptive machining adjusts cutting parameters on the fly, ensuring consistent quality even with complex geometries. For shops producing aerospace or medical components, this level of CNC precision is a game-changer. As smart factories become the norm, expect AI to be a cornerstone of CNC manufacturing across Canada and the U.S.
The Rise of Automation in CNC: Lights-Out Manufacturing
Automation in CNC is no longer a luxury—it’s a necessity. With labor shortages impacting North American manufacturers, CNC trends 2025 point to widespread adoption of robotic arms, cobots (collaborative robots), and automated material handling systems. These technologies enable “lights-out” manufacturing, where CNC machines run 24/7 with minimal human intervention.
For instance, a robotic loader can feed raw materials into a 5-axis CNC machine overnight, boosting output by 20–40%, based on recent automation case studies. This is particularly valuable for high-mix, low-volume production, where flexibility is key. By integrating automation in CNC, shops can address labor challenges while meeting tight deadlines, making it a top trend to watch in North American CNC markets.
5-Axis and Beyond: Precision Meets Versatility
The shift to 5-axis CNC machines is accelerating as manufacturers demand greater versatility and CNC precision. Unlike traditional 3-axis machines, 5-axis systems can machine complex parts in a single setup, reducing cycle times by up to 50%, per industry benchmarks. This is critical for industries like aerospace, where intricate turbine blades require exacting standards.
Looking ahead, CNC trends 2025 suggest 6-axis machines and hybrid systems (combining subtractive and additive processes) will gain traction. These machines cater to the growing demand for lightweight materials like composites, used in electric vehicles and renewable energy systems. For CNC manufacturing businesses, investing in 5-axis CNC or hybrid systems is a strategic move to stay competitive.
Sustainable CNC: Greener Manufacturing Practices
Sustainability is a driving force in CNC machining as environmental regulations tighten and customers demand eco-friendly solutions. Sustainable CNC practices, such as energy-efficient machines and waste reduction, are becoming standard in 2025. For example, modern CNC systems use variable-frequency drives to cut energy consumption by 15–25%, according to equipment manufacturers.
Additionally, digital twins—virtual replicas of CNC machines—help optimize toolpaths, reducing material waste by up to 20%. Shops are also adopting closed-loop coolant systems to minimize environmental impact. In North American CNC markets, where sustainability is a priority, these sustainable CNC innovations are attracting eco-conscious clients in industries like automotive and renewable energy.
IoT and Smart Factories: Connected CNC Systems
The Internet of Things (IoT in manufacturing) is transforming CNC machining by enabling real-time monitoring and data-driven decisions. In 2025, smart factories will rely on IoT sensors to track machine performance, tool wear, and production metrics. This connectivity allows shop managers to access data remotely, improving efficiency and reducing downtime.
For example, IoT-enabled CNC technology can send alerts when a tool is nearing the end of its lifespan, preventing costly defects. A 2024 study by a leading manufacturing journal found that IoT integration improved overall equipment effectiveness (OEE) by 10–15% in CNC shops. As Industry 4.0 advances, IoT in manufacturing will be a defining trend for CNC manufacturing in Canada and the U.S.
Additive and Subtractive Synergy: Hybrid CNC Machines
The line between additive manufacturing (3D printing) and CNC machining is blurring, thanks to hybrid machines. These systems combine additive processes (building parts layer by layer) with subtractive CNC precision (cutting and milling), offering unmatched flexibility. In 2025, hybrid machines will be critical for industries like aerospace and medical, where complex geometries and lightweight materials are in demand.
For instance, a hybrid machine can 3D-print a near-net-shape part and then use 5-axis CNC to finish it to tight tolerances, cutting production time by 30%, based on recent case studies. This synergy is a key CNC trend 2025, enabling manufacturers to innovate faster and reduce costs.
Digital Twins: Virtual Precision for Real-World Results
Digital twins are virtual models that simulate CNC machines and processes, allowing manufacturers to test setups and optimize workflows before cutting metal. In 2025, digital twins will be widely adopted in CNC manufacturing to reduce scrap rates and improve efficiency. By simulating toolpaths, shops can identify errors early, saving time and materials.
A 2024 industry report noted that digital twins reduced setup times by 25% in advanced CNC shops. For North American CNC businesses, this technology is a cost-effective way to enhance CNC precision and compete in high-stakes industries like defense and electronics.
Why These Trends Matter for Your Business
The CNC machining landscape in 2025 is all about embracing Industry 4.0 technologies—AI, automation, IoT, and digital twins—while prioritizing sustainability and versatility. These CNC trends 2025 are not just buzzwords; they’re proven solutions driving real results. For example:
- AI in CNC and IoT in manufacturing reduce downtime and boost productivity.
- Automation in CNC addresses labor shortages, a pressing issue in North America.
- Sustainable CNC practices attract eco-conscious clients and comply with regulations.
- 5-axis CNC and hybrid machines meet the demand for complex, high-precision parts.
By staying ahead of these trends, CNC manufacturing businesses can improve efficiency, cut costs, and deliver superior products. Whether you’re machining aerospace components in Toronto or automotive parts in Detroit, adopting these CNC technologies will position your shop for success.
How to Prepare for the Future of CNC Machining
Ready to embrace the CNC trends 2025? Here are three steps to get started:
- Invest in Training: Upskill your team on AI in CNC, IoT in manufacturing, and 5-axis CNC programming to maximize new technologies.
- Evaluate Equipment: Consider upgrading to energy-efficient CNC machines or hybrid systems to boost versatility and sustainability.
- Partner with Experts: Work with a trusted CNC technology provider to integrate automation in CNC and digital twins into your workflow.
The future of CNC machining is bright, and 2025 is the year to seize these opportunities. Stay informed, stay innovative, and let smart factories lead the way.
Disclaimer
The information provided in this article is for informational purposes only and reflects current industry trends and insights as of May 2025. It is not intended as professional advice. Before implementing any changes to your CNC machining processes or equipment, consult with industry experts or qualified professionals to ensure suitability for your specific needs.